Precision CNC Machining Manufacturer: Elevating Your Business with Quality Fabrication
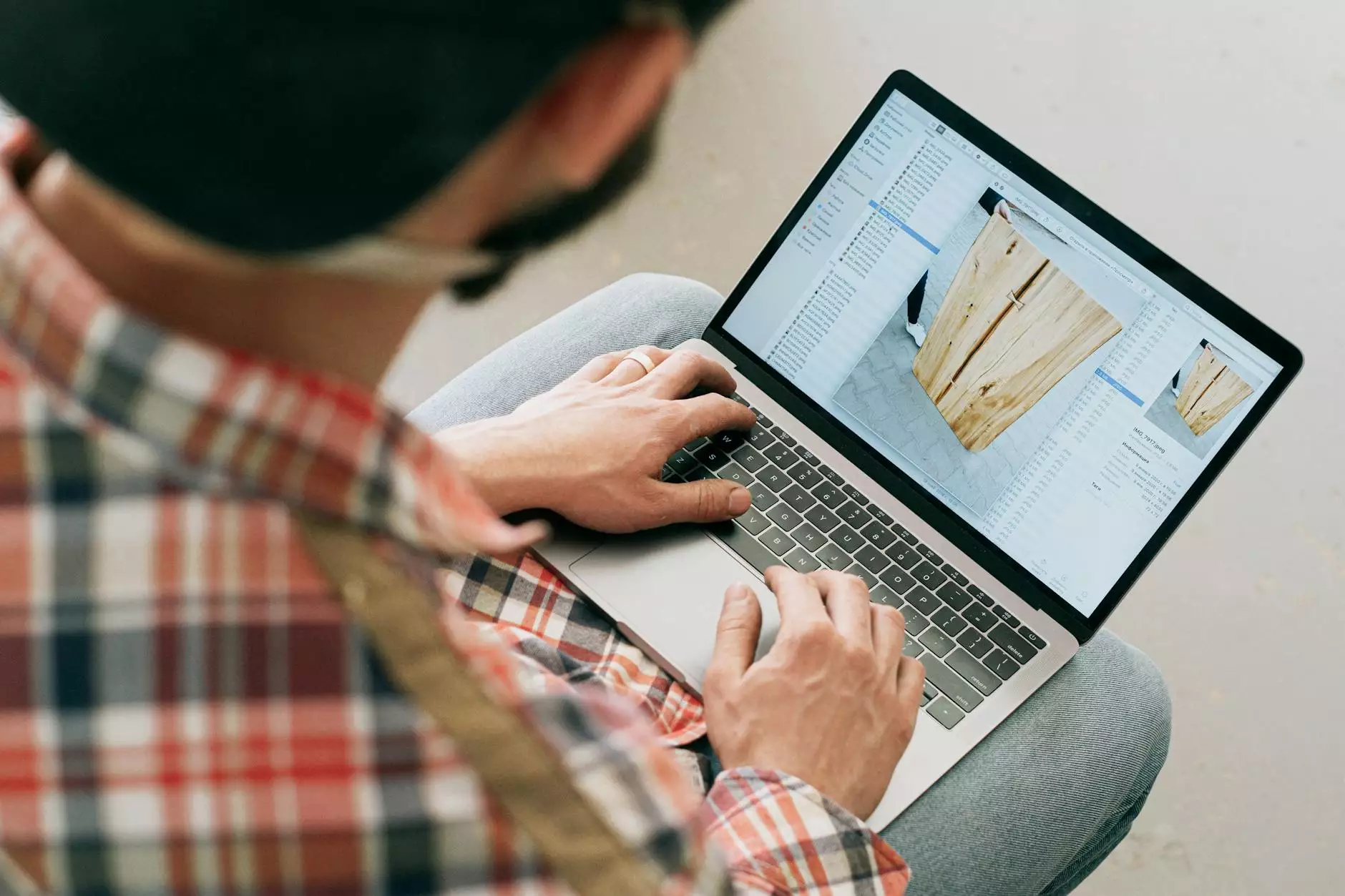
CNC machining, or computer numerical control machining, represents a groundbreaking development in manufacturing technology, offering unparalleled accuracy and consistency. As a precision CNC machining manufacturer, DeepMould is dedicated to delivering the highest quality metal fabrication services. In this article, we will explore the significance of CNC machining, its vast applications, and how it can greatly benefit businesses across various sectors.
Understanding CNC Machining
CNC machining involves the use of computers to control machine tools, enabling the production of intricate parts and components with maximal precision. The benefits of CNC machining are numerous:
- High Precision: Offers dimensions and tolerances that are exceedingly tight, ensuring that components fit perfectly in assembly.
- Increased Efficiency: Automated machining processes allow for rapid production, significantly reducing lead times.
- Repeatability: Once a machining process is programmed, it can produce the same part repeatedly with minimal variance.
- Complex Geometries: Capable of creating intricate shapes that would be difficult or impossible to achieve by hand.
Applications of Precision CNC Machining
CNC machining is versatile and caters to a wide range of industries, including but not limited to:
- Aerospace and Defense: Manufacturing high-performance parts that require lightweight materials and stringent standards.
- Automotive: Producing components that enhance vehicle performance, safety, and aesthetic value.
- Medical Devices: Creating precise and critical components for life-saving and life-enhancing devices.
- Electronics: Fabricating housings, connectors, and various components with high precision.
- Industrial Equipment: Manufacturing parts that meet high levels of durability and performance for machinery.
Why Choose DeepMould as Your Precision CNC Machining Manufacturer
When it comes to selecting a precision CNC machining manufacturer, not all options are created equal. Here are several reasons why DeepMould stands out:
1. Expertise and Experience
With years of industry experience, DeepMould has honed its skills and expertise in CNC machining, ensuring quality at every stage of the manufacturing process. Our team is composed of skilled professionals who are well-versed in the latest technologies and techniques.
2. State-of-the-Art Equipment
DeepMould utilizes the latest CNC machines equipped with advanced technology to achieve the highest levels of precision and efficiency. Our investment in cutting-edge machinery ensures that we can handle even the most complex projects with ease.
3. Quality Assurance
Quality is at the core of what we do. From the initial design phase to the final inspection, we employ rigorous quality control measures to ensure that every part we produce meets the highest standards. Our certifications, including ISO, demonstrate our commitment to quality.
4. Custom Solutions
We understand that every client has unique needs. Our approach as a precision CNC machining manufacturer is to provide custom solutions tailored to the specifications of your project. Whether you require specific materials, finishes, or geometries, we are here to assist.
5. Commitment to Timely Delivery
In today’s competitive landscape, time is money. DeepMould is dedicated to meeting project deadlines without compromising quality. Our streamlined processes ensure that your orders are delivered on time, every time.
The CNC Machining Process: A Step-by-Step Overview
Understanding the CNC machining process is essential for businesses looking to leverage its benefits. Here’s a detailed breakdown:
Step 1: Design and Prototyping
The journey begins with design. Using CAD (Computer-Aided Design) software, engineers create detailed models of the parts to be produced. Prototypes can also be generated to test functionality before mass production.
Step 2: Material Selection
Choosing the right material is crucial for ensuring that the end product meets the required performance characteristics. Common materials include aluminum, stainless steel, titanium, and plastic.
Step 3: Tool Path Creation
Once the design and materials are determined, programmers develop a tool path using CAM (Computer-Aided Manufacturing) software. This outlines every movement the CNC machine will perform.
Step 4: Machining
During the machining phase, the CNC machine executes the programmed tool paths, cutting the material into the desired shapes and sizes with remarkable precision.
Step 5: Finishing and Inspection
After machining, parts may undergo various finishing processes, such as polishing, anodizing, or coating. Inspections are then carried out to ensure that the parts adhere to exact specifications and quality standards.
The Future of CNC Machining in Metal Fabrication
The landscape of manufacturing is ever-changing, and CNC machining is at the forefront of these innovations. As a precision CNC machining manufacturer, DeepMould is excited about the future, where advancements include:
- Automation and AI: The incorporation of artificial intelligence into CNC machining for smart manufacturing solutions.
- 3D Printing and Hybrid Manufacturing: Combining CNC machining with additive manufacturing techniques for even greater design flexibility.
- Sustainable Practices: Increasing emphasis on eco-friendly materials and processes to minimize environmental impact.
- Enhanced Software Technologies: Improvement in CNC programming software leading to better machine performance and part design.
Conclusion
In summary, selecting a precision CNC machining manufacturer like DeepMould can significantly enhance your production capabilities. By understanding the processes, benefits, and future possibilities of CNC machining, businesses can position themselves to thrive in competitive markets.
At DeepMould, we are committed to providing our clients with the highest quality CNC machining services and are ready to collaborate on your next project. Contact us today for customized solutions that align with your business objectives.